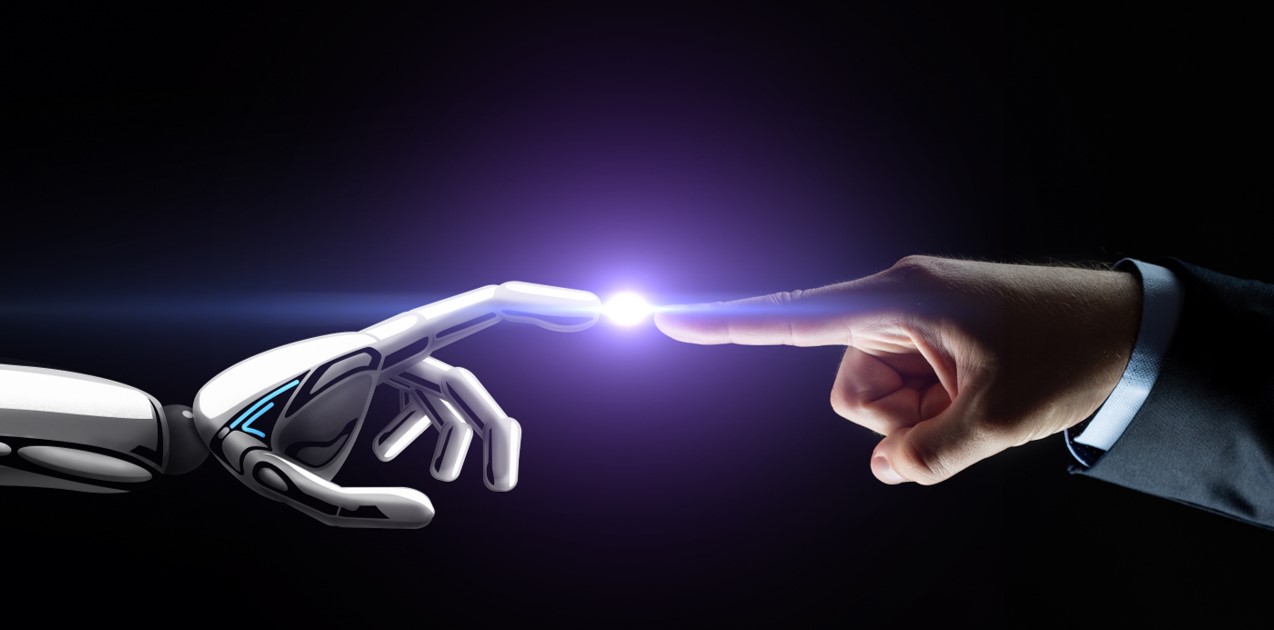
Industrial Networking and Automation: Terminology, Part 3 (Control Systems, PLC, and DCS)
By Tom Carpenter On 02/24/2021
Control systems have been key to the development of industrial automation. A control system is used to control the output of a machine or other system to meet requirements based on a sequence of events or a specified condition. This article will address control systems in general and PLC and DCS systems specifically.
Within industrial automation, a control system is used for three primary categories of control (Instrumentation and Control Systems, Second Edition, William Bolton, 2015):
- Controlling Variables: Examples include temperature, pressure, fill level, size of machined objects, weight, and more. The control system can adjust heat levels, flow levels, and other factors to achieve the desired output (temperature, pressure, etc.).
- Controlling Sequences: The sequence of events is controlled based on the results or feedback from other events. For example, a conveyor belt may transport a part into a machine and stop until the machine is finished with its processing. If the machine is successful at achieving the desired results, the part is moved out of the machine and to the next phase and the next part is moved into the machine. If a failure occurs in the machine, the part is discarded or an alert is triggered. The sequence of events is controlled by the control system that monitors the systems and processes. Additionally, the actual sequence of events may be defined by the control system dependent on settings. William Bolton gives the example of a washing machine with the setting to "whites". The machine is activated for a specific sequence based on the control system, which is configured for "whites". If the setting is changed to "towels", a different sequence is initiated by the control system.
- Controling Event Occurrence: In some cases, an event should not occur unless a control system releases it to occur. The example of the waching machine fits here as well. The door lock on the washing machine acts as the control system preventing the wash from starting unless the door is closed. This control systems is particularly important for a front load waching machine.
A complex control system may indeed use all three categories of control or some combination of them.
In this context of industrial automation, a system can be defined as any unit that receives input and produces output. The concern of control is the output of each system, which may demand control of the input as well. As an analogy, consider a water filtration system in your home. The input is unfiltered water and the output is filtered water. You may not understand or care about the actual filtration process that occurs within the system. You are, however, concerned with the output being "better" than the input. The system may use one filter or it may use several filters. You care only that the output has fewer contaminants in it than the input had originally.
Industrial automation may include systems that machine parts, assemble components, heat elements, cool elements, and more. The control system ensures that these industrial systems are operating such that the output is as desired. The control system may be localized or distributed. A localized control system is like that in a washing machine (considering traditional machines and not those with IoT-enabled remote control). A distributed control system indicates that the parameters of control can be defined from a remote location at the same site or even another site.
Two types of control systems are used within industrial implementations: open-loop and closed-loop. Open-loop control systems receive no feedback from the output, they simply control the input based on a defined value or set of values. Closed-loop control systems do monitor and receive feedback from the output allowing for dynamic adjustments to the input in the achievement of the desired output.
To make is as simple as possible, think of an open-loop control system as one configured to pour 12 ounces of fluid into each container that passes by on a conveyor belt. Thinkg of a closed loop system as one that is configured to pour fluid into a container until it reaches a defined level and the level is monitored during filling. The level is fed back to the input and causes the flow to stop once the level is reached. Open-loop control systems are less expensive and are, therefore, useful in many scenarios when feedback is not required. In a later article, I'll discuss the details of how closed-loop control systems are schematically defined and mechanisms used to implement them.
Now that you understand the basics concelts of control systems, you can explore two implementations for managing them: programmable (or progammed) logic controler (PLC) and distributed control system (DCS).
A PLC is a computer-based controller that allows for simplified programming of logic, resulting in the control of industrial (or other) machinery. The washing machine example given previously proves useful here. A microprocessor is used in the modern waching machine to enable different motors at different speeds and open different valves at different levels and all at different times depending on the settings configured on the washer. The PLC differs in that it can be reprogrammed by the engineer to perform different functions. For example, one run through a process may be filling bottles that hold 12 ounces of liquid and the next run will be filling bottles that hold 20 ounces of liguide. The program on the PLC can simply be changed to manage these differences.
Productivity1000 Stackable Micro PLC (Source: AutomationDirect.com)
It is a logic controller because the program effectively says if A then B, or if A and B then D, or if A not B then C, etc. In general terms, the PLC receives input from sensors and provides output to actuators. The internal logic is used to control the actuators based on the program instructions and, possible, input from the sensors. The IEC 61131 standard defines network communication blocks that can be used to standardize the communications within and between PLC systems. These include communications such as:
- CONNECT
- READ
- WRITE
- NOTIFY
- STATUS
A common programming method for PLCs is ladder programming (LAD). LAD uses ladder diagrams to define the operations of the program. It can be implemented as a sort of visual programming where switching circuits are drawn to define the process. While it is beyond the scope of this article (and series) to go far beyond terminology definitions, a good resource is Willam Bolton's book, Programmable Logic Controllers, Sixth Edition.
PLC networks may be constructed that allow PLCs to communicate with other computer systems, the Internet, and other PLCs. This option allows for centralized control and management of all PLCs.
The line between PLCs and DCS solutions have been blurred in recent decades due to the use of PLC networks; however, a fundamental difference is that a PLC is technically a standalone control programmed for a specific task (source: Difference Between DCS and PLC) where DCS solutions function as control systems that work through multiple levels to achieve the end result. According to instrumentationtools.com, DCS solutions were designed to control processes and not discrete operations. Another key difference between PLCs and DCSs originally was that PLCs use the ladder logic programming and DCSs use the function block programming. However, that has even changed today as PLCs often support function block programming as well.
The general differences in use between PLCs and DCSs is summarized by Automation World (https://www.automationworld.com/products/control/article/13311313/plc-vs-dcs-which-is-right-for-your-operation) as follows:
- Response Time: PLCs are generally faster and more suitable for real-time safety critical scenarios.
- Scalability: DCSs are generally more scalable, though PLCs can be scaled through PLC networks and can be more complicated than DCSs when scaled.
- Redundancy: DCSs, while not technically more redundant in capabality (multiple redundant PLCs can be used), are typically more cost-effective when redundancy is required.
- Complexity of System: More complex systems tend toward the use of DCSs and less complex systems tend toward the use of PLCs.
- High Variability in Processes: PLCs are best used when the process does not change frequently and DCSs are more suited for this.
In the next article within the terminology series, we'll address remote control and management through the use of SCADA systems. When you finish reading the series, you will have a good foundational knowledge of the technologies and terminology used in industrial networking and automation, which will help you better integrate wireless IIoT solutions into these spaces.
Tagged with: IIoT, Industrial IoT, Networking, Automation, Control System, PLC, DCS
Blog Disclaimer: The opinions expressed within these blog posts are solely the author’s and do not reflect the opinions and beliefs of the Certitrek, CWNP or its affiliates.